Global Challenges Drive Innovation at Pannonia Bio’s Ethanol Plant
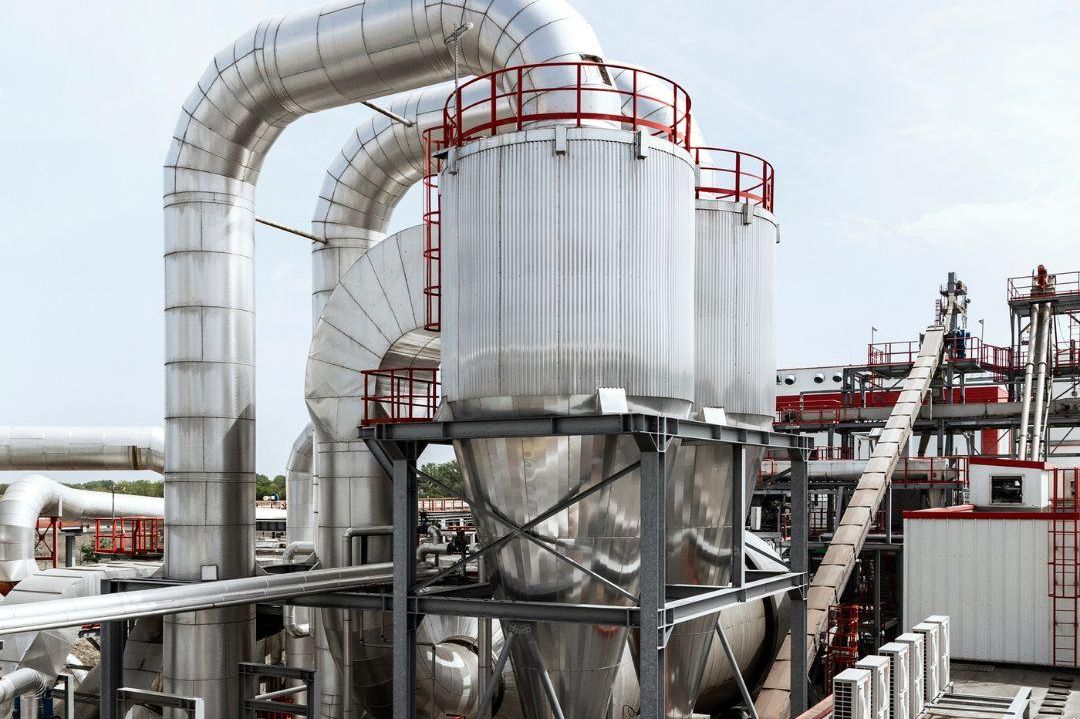
Pannonia Bio's ethanol plant not only leads in green innovation but exemplifies collaborative success. Since 2012, the company has grown into Europe's largest ethanol facility, with Vahterus playing a pivotal role in its transformative journey towards one of the most efficient refinieries in the world.
Since 2012, Pannonia Bio operates a biorefinery in Dunafoldvar, Hungary. The biorefinery is the largest ethanol plant in Europe, one of the most efficient refineries in the world, and has a mission to mitigate climate change.
According to Pannonia Bio, the production of bioethanol is one of the most cost-effective ways to reduce greenhouse-gas emissions. Since 2011, the average certified greenhouse-gas emission savings of renewable ethanol against fossil fuel have increased continuously, reaching 70% in 2017, reports ePure, an organisation that speaks for renewable ethanol producers in Europe.
Pannonia Bio is constantly improving its processes and is a nursery for the development of new bio-based technologies. From its beginning as a bioethanol producer in 2012, the refinery has almost tripled in size and developed into a multiproduct facility, where nutrition, health, biochemical and fuel bioproducts are manufactured as alternatives to products made from fossil based materials.
‘We’re always pushing for improvement in operation and efficiency. That‘s the most fascinating part of this job’, says Michael Healy, the Principal Technical Consultant of Pannonia Bio, who has been with the company since 2012.
Born in Dublin, Ireland, Healy was always interested in technology as a youngster. In college, he studied engineering and graduated in Mechanical Engineering. After graduate training with Guinness in Dublin, he worked in the oil and gas business in Canada for several years. Most of his career has been spent with GEA in the process industry – breweries, food industry, biotech and pharma industries – with projects all over the world. After a successful international career, he remains eager to learn more, and Pannonia Bio has been the perfect platform.
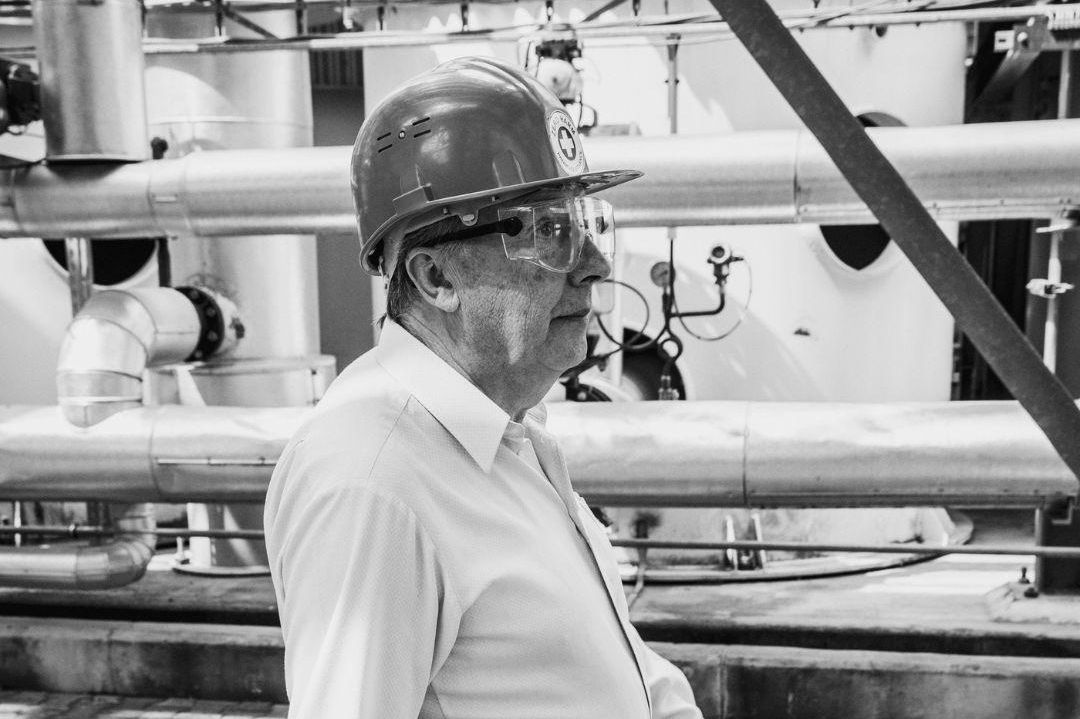
Located in the heart of Hungary’s corn-growing region, close to the town of Dunafoldvar, the refinery processes over a million tons of feed corn annually to produce 325,000 tons of protein-rich animal feed, 500 million litres of bioethanol and 12,000 tons of corn oil. Family farming is a major economic activity in an area that, after the international recession in 2008, was left one of the most disadvantaged regions in Hungary. The plant has made a significant positive social and economic impact on the town of Dunafoldvar by creating new steady jobs, helping to keep skilled labour in place and mitigating selective migration.
Pannonia Bio does business with hundreds of corn farmers and has fundamentally improved their livelihoods. Predictable demand for corn reduces risks and stabilises prices. Research shows that the plant has also contributed to improved payment discipline in the corn market.
‘It’s wonderful to see a farmer being able to harvest his corn and take it with his own truck to our plant and get paid in a few days’ time’, says Mark Turley, the Founder of Pannonia Bio. The company continuously seeks opportunities to strengthen local partner relations, contributing nearly 500 million euros to Hungary’s GDP and supporting over 3,000 jobs, mostly in rural communities.
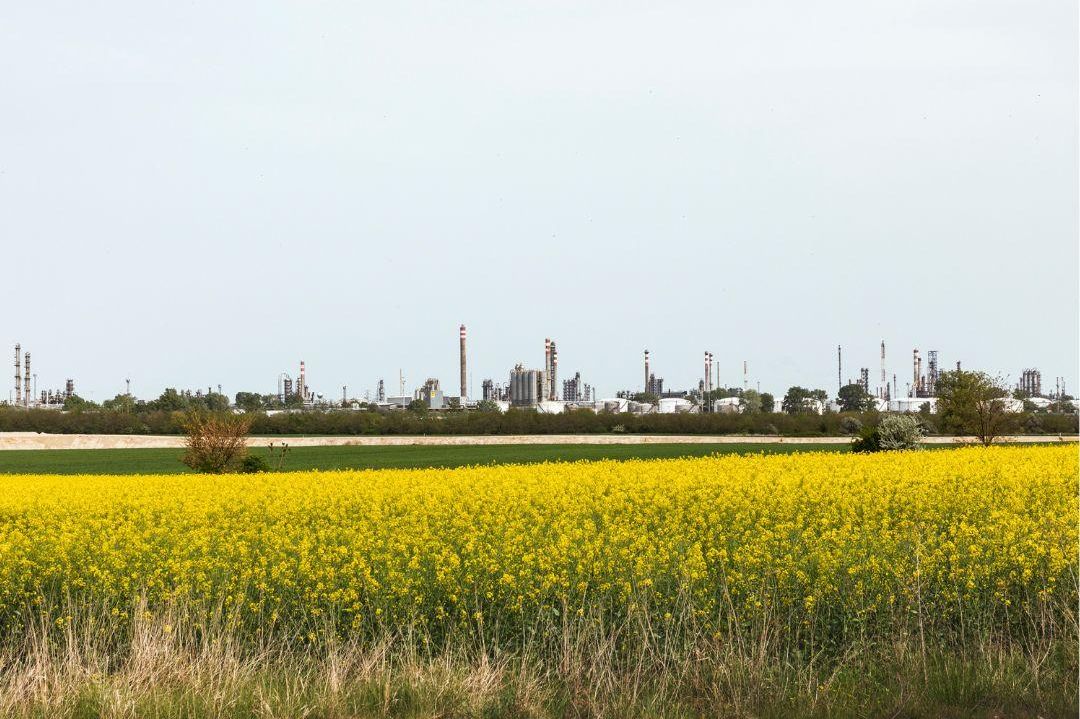
Currently, about 80% of Pannonia Bio’s annual ethanol output is used for blending with gasoline employed in transportation. Transportation is the second biggest source of carbon emissions in the European Union, and by 2020 the EU aims to make 10% of the transport fuel of every EU country come from renewable sources such as biofuels.
Fuel suppliers are also required to reduce the greenhouse-gas intensity of the EU fuel mix by 6% by 2020 in comparison to 2010. The EU has set rigorous sustainability criteria for biofuels and bioliquids to ensure that the decrease of greenhouse gas emissions comes without adverse effects on the environment or social sustainability.
Pannonia Bio has met, or out-performed all the EU’s climate, energy, feed, water and air pollution standards and regulations. At the plant, new technological innovations continue to be implemented in order to improve efficiency, minimise waste and reduce water consumption. This is also how the collaboration between Vahterus and Pannonia Bio began.
In late 2017, Pannonia Bio was planning a major change in its existing process, which required a steam generator to recover heat energy from ethanol vapour. In the new process, hot ethanol vapours would be used for boiling hot water to make low pressure steam, which is the energy source for the stillage evaporation system.
Pannonia Bio evaluated different heat exchanger technologies including Shell & Tube type, Plate only and Plate & Shell type, but the 14-week delivery time turned to Vahterus’ advantage: the timeframe would have been too tight for the Shell & Tube heat exchanger. Footprint was also limited because the heat exchanger was to be installed on the roof of the plant building.
‘The Vahterus design was ideal for this job. It has a fully welded design on the ethanol vapour side and is very compact’, Healy explains.
The heat exchanger was purchased in January 2018 and was delivered in April 2018, just in time for installation during the plant’s spring shutdown. The 16t steam generator was installed on the roof using a 400t crane. The purpose of the unit is to generate 1.2 bar(a) steam using 5 bar(a) ethanol.
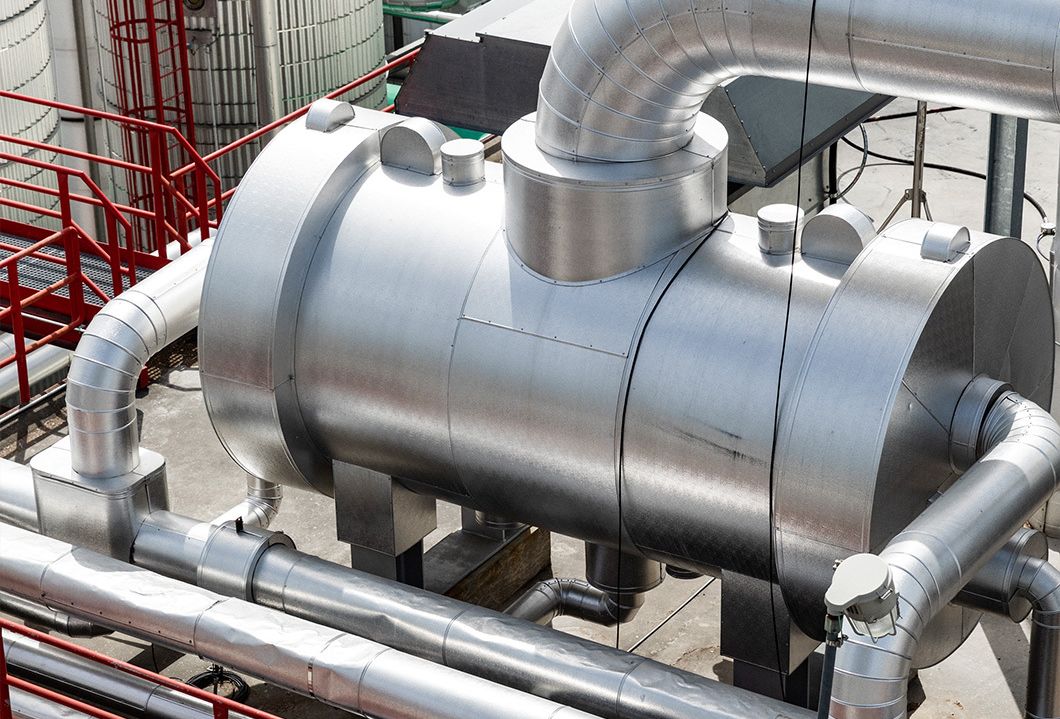
After a full year of the new process running, Healy is genuinely happy about the collaboration with Vahterus. The heat exchanger has performed according to plan and working with Vahterus has been effortless.
‘They’re all fantastic people’, he says, ‘and that’s what makes the difference. Whether it’s building a team or finding the right collaborators for your business, once everyone has the proper skillset, it all comes down to people and their attitude’.
Cooperation between the two companies continues, and earlier this year, ten new Vahterus heat exchangers were installed at the plant as part of another process expansion: ‘These are much smaller than the big unit installed last year. I’m sure we’ll have many suitable heat exchanger applications in the future’, Healy says.
In less than a decade, Pannonia Bio has entered a new market and developed into the largest ethanol plant in Europe. The future for Pannonia Bio’s business is continuous improvement in its process, reduced energy consumption and even greater greenhouse-gas savings. The company also intends to further diversify its product portfolio to reduce its dependence on fuel ethanol.
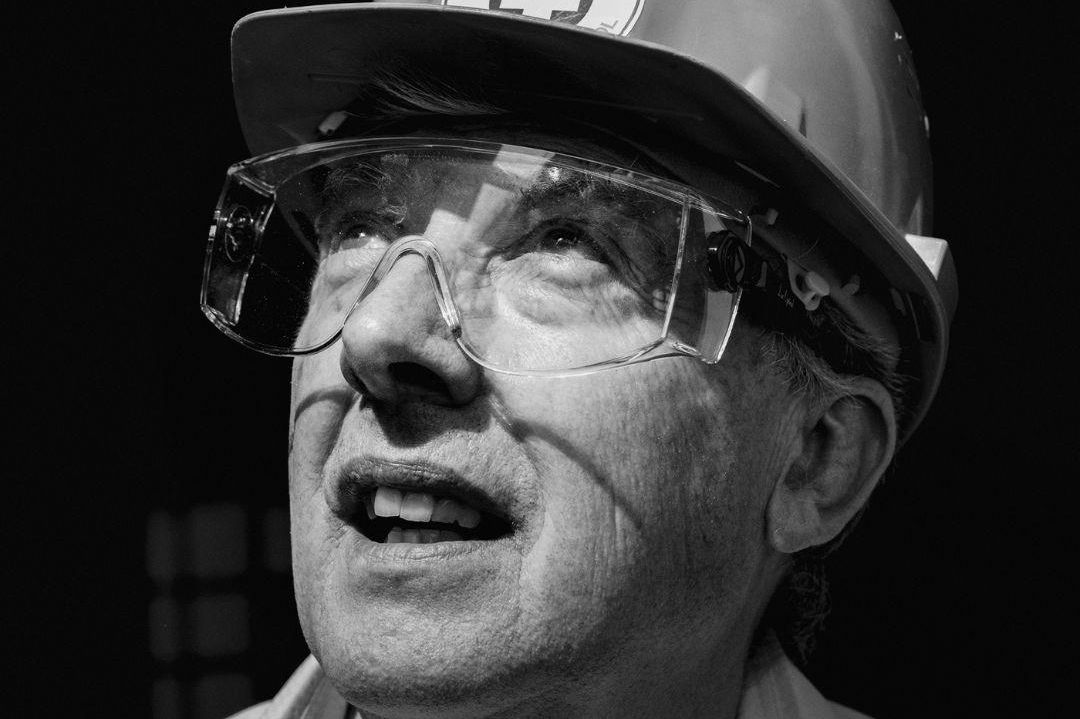
When Healy mentions his long-time fascination with Roman history, it’s tempting to look for similarities between the pioneering civilisation and his own mindset and choice of career.
‘When the Roman Empire broke down, development not only stopped, but Europe went back in time. The Romans were ahead of their time. They were civilised, innovative and also great engineers. I admire their organisational skills and their ability to globalise ideas’, Healy says.
At Pannonia Bio, innovative biotech concepts are supported with engineering expertise to bring them to commercial scale, and the development has been fast. One simple recipe for a success story: start with a good idea, and add in a team of excellent engineers.
Pannonia Bio is a subsidiary of ClonBio Group Limited, an Irish agribusiness headquartered in Dublin, Ireland.
Download the case study as a PDF
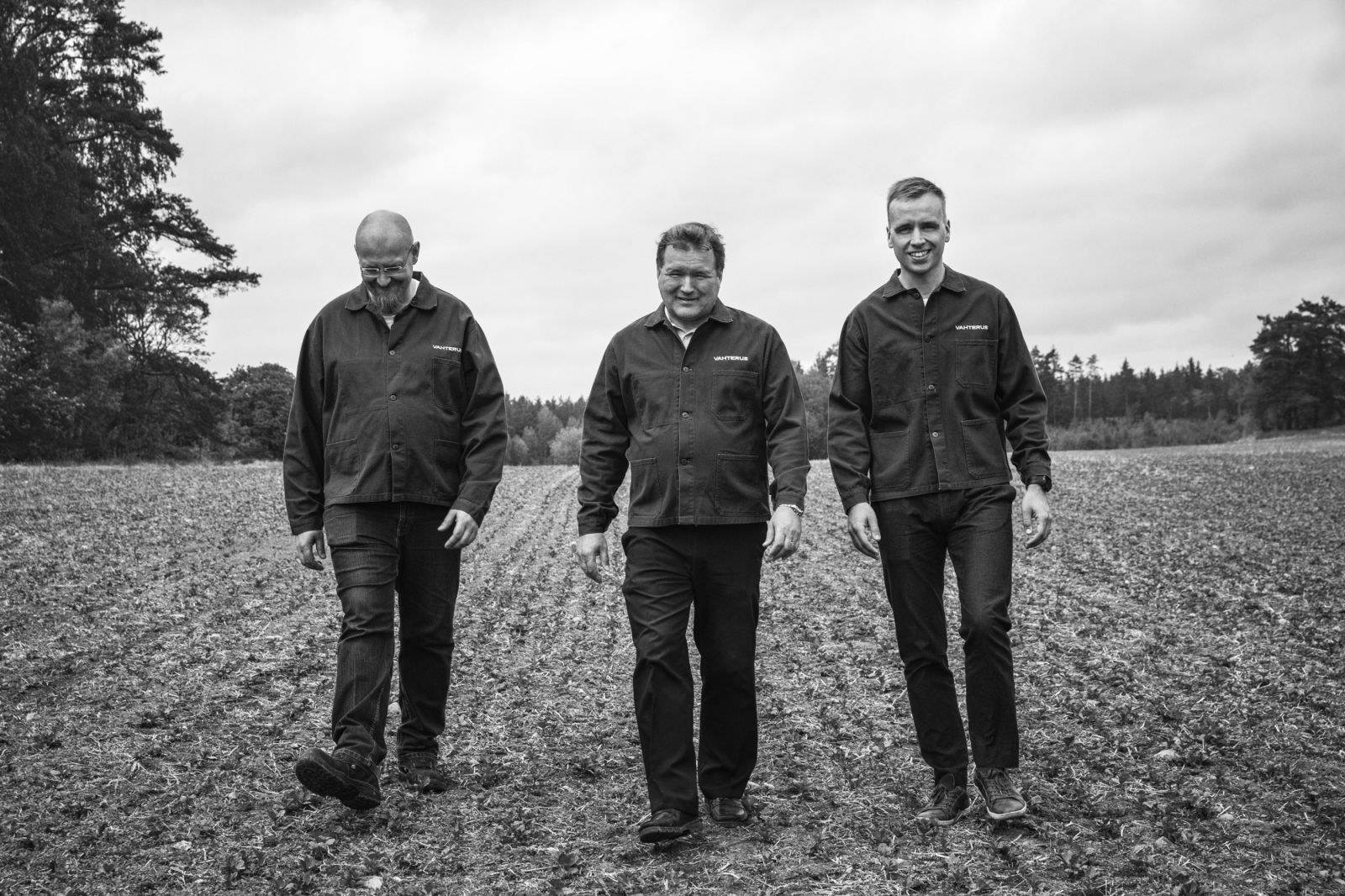
Transform your project with Vahterus Expertise
Interested in working with us? Our team of experts are ready to collaborate with you. Contact us today to embark on a journey towards cost-effective, sustainable and energy-efficient heating solutions.
Discover more of our Customer Stories
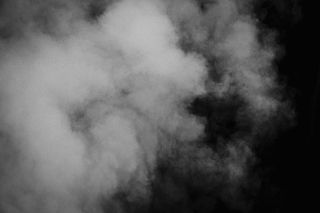
Cryostar’s Saturation System Transforms Truck-Fuelling Stations
Founded in 1972, Cryostar specialises in designing and manufacturing cryogenic equipment. The company offers turbomachines, gas heaters and vaporisers, pumps, turbines as...
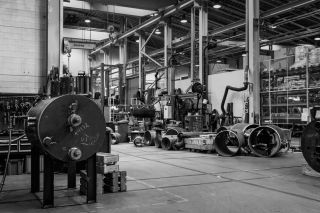
Colonial Pipeline Runs Between the Gulf Coast and the New York Harbor Area
Colonial Pipeline, headquartered in Alpharetta, Georgia, is the largest US refined products pipeline system and can carry more than three million barrels...
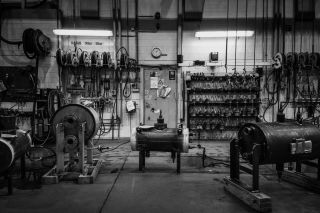
Entering Into Low-Carbon Economy Utilising Cold Energy Recovery
The production of alcohol amines requires large amounts of ethylene. A chemical plant in Eastern China specialises in alcohol amine production. Ethylene...